Kütləvi istehsal adından məlum olduğu kimi toplu formada istehsala deyilir. Lean Six Sigma isə iki komponentdən ibarətdir: Lean (Yalın) + Six Sigma (Altı Siqma). Yalın istehsal (Lean production) bütün komandanın müştərək işləməsinə əsaslanan, sistematik olaraq israfların aradan qaldırılmasını hədəfləyən bir Uzaq Şərq fəlsəfəsidir. Yapon şirkəti Toyotanın tətbiq etməsi ilə yalın istehsal bütün dünyada şöhrət qazanmağa başladı. Altı Siqma isə Amerikanların icadı sayılır; 1986-cı ildə Motorolanın tətbiq etməsi ilə bütün sənayelərdə diqqət çəkməyə başladı. Bu iki metodun birgə tətbiqi nəticəsində minlərlə şirkət gəlirlərdə artım, xərclərdə ciddi azalma əldə etdilər. Bu gün də bu metodlar dünya miqyasında tətbiq edilir və böyük şirkətlər öz işçilərini Lean Six Sigma (LSS) üzrə inkişaf etdirirlər, onlardan şirkətdəki prosesləri optimallaşdırmağı gözləyirlər.
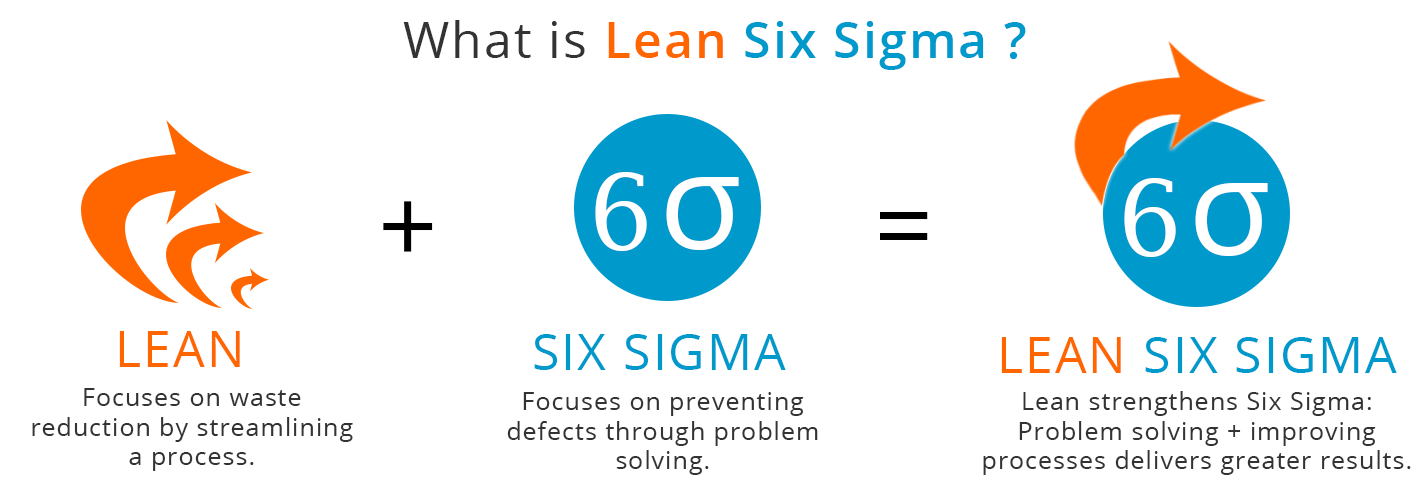
Kütləvi İstehsalın tarixi isə daha köhnədir. 19-cu əsrin sonlarından Ford şirkəti sayəsində dünyaya yayıldı. Onun dövrünə görə öz üstünlükləri vardı, amma bu gün həmin metod köhnəlmiş sayılır. Bu yazıda LSS və kütləvi istehsal arasındakı fərqlərdən bəhs edəcəyik. Eləcə də LSS-in şirkətlərdə səmərəliliyi necə artırması barədə danışacağıq.
Kütləvi İstehsaldan fərqli olaraq Yalın istehsal tələbdəki trendə uyğun istehsala əsaslanır. Bunlar arasında əsas dörd fərq var:
• Kütləvi istehsal böyük ölçülü lotlarla istehsal etmək deməkdir. Məqsəd bir lotda mümkün qədər çox məhsul istehsal etməkdir. Yalın istehsal isə bazardakı tələbə uyğun olaraq istehsal etməkdir. Məsələn, əgər bahalı bir maşına bazarda tələbat azdırsa, onu tamamilə sifariş əsaslı istehsal etmək olar.
• Kütləvi istehsal nəticəsində məhsullar anbarlarda saxlanılır, sonra distribyutorlara göndərilir və oradan da pərakənda satıcılara yönləndirilir. Daha sonra yekun müştəri onlardan malı alır. Yalın istehsal isə aralıq mərhələləri (distribyutor, pərakəndə satıcı) qəbul etmir və əsasən birbaşa müştərilərlə işləyir.
• Kütləvi istehsalın planlaşdırılması mürəkkəb prosesdir və bir çox faktorlardan asılıdır (inventar səviyyəsi, qiymət, tranzit müddəti və s.). Bunun üçün xüsusi planlaşdırma proqramları tələb olunur.
• Kütləvi istehsal itələmə sistemidir – istehsal edib bazara yerləşdirirsiniz, müştəri oradan alır məhsulu. Yalın istehsal isə çəkmə sistemidir – istehsalı müştəri tələbinə əsaslanaraq edirsiniz.
LSS bütün istehsal və təchizat prosesindəki fəaliyyətləri iki qrupa bölür: dəyər yaradan və dəyər yaratmayan. Dəyər yaradan fəaliyyətlər müştərinin pul ödəməyə hazır olduğu proseslərdir. Məsələn, elektrik generatoru istehsal edən firma üçün metalın işlənməsi (onun müxtəlif formalara salınması) müştəri üçün dəyər yaradan prosesdir. Amma tutaq ki, generatorun hissələrinin montaj üçün zavodun bir tərəfindən digər tərəfinə daşınması müştəri üçün dəyər yaratmır. O sizin daxili prosesinizdir, mümkündürsə bölmələri bir-birinə yaxın yerləşdirərək bu fəaliyyətdən xilas ola bilərsiniz.
Kütləvi istehsal çoxlu miqdarda israfla nəticələnir. LSS üçün əsas yeddi növ israf var:
1. Lazımından artıq istehsal. LSS metodologiyasında tələb olunandan artıq istehsal etmək israf sayılır. Çünki istehsal bitdikdə o məhsulların müştərisi məlum olmur (ümumiyyətlə satılıb-satılmayacağı məlum olmur). Bu da özlüyündə risk daşıdığı üçün LSS-də israf sayılır.
2. Gözləmə. İstehsal prosesinin mərhələləri arasında gözləmə müddətləri, avadanlığın istifadəsiz qalması, montaj prosesində işçilərin hansısa bir hissəni gözləmələri israf edilən vaxtdır.
3. Nəqliyyat. Lüzumsuz olaraq məhsulların və ya onların hissələrinin zavodun bir hissəsindən digərinə daşınması və ya hazır məhsulun distribyutorlara göndərilməsi, onun geri qaytarılması bu növ israfa aiddir.
4. İnventar (stok). Yuxarıda da bəhs etdiyimiz kimi, əgər məhsullar istehsal edilib anbara yığılırsa onların satılmama, xarab olma, forklift tərəfindən əzilməsi riski var.
5. Hərəkət. İnsanların və ya avadanlıqların lüzumsuz yerə hərəkət etmələri də israf sayılır.
6. Lazımından artıq emal. Əgər bir məhsulun ərsəyə gəlməsi üçün bir saat kifayətdirsə və həmin məhsul istehsalda ondan artıq vaxt keçirirsə, bu israfdır.
7. Defektlər. Təbii ki, əgər istehsal nəticəsində defektli mallar istehsal olunursa, bu, prosesdə olan problemlərdən xəbər verir və israfın 7-ci növünü təşkil edir.
LSS-in bir metodologiyası olan Total Məhsuldar Texniki Xidmət (TMTX) mükəmməl istehsalı təmin etmək üçün holistic bir yanaşmadır:
• Sıfır xarabolma
• Sıfır dayanma
• Sıfır defect
• Sıfır qəza.
TMTX proaktiv olaraq profilaktik (önləyici) texniki xidmət göstərməklə əməliyyatların səmərəliliyini mümkün olan ən yüksək səviyyədə saxlamağı nəzərdə tutur. Bu yanaşmada işçilər və operatorlar tək istehsala yox, həm də texniki xidmətin bir hissəsinə cavabdeh olurlar. Operatorlara təlim verilir və onlar kiçik xarabolmaları aradan qaldırmağı öyrənirlər. Belə olduqda texniki xidmət şöbəsinin personalı hər kiçik prosesə müdaxilə etmək məcburiyyətində qalmırlar. Həm də boşdayanma müddəti minimum endirilmiş olur. TMTX məsuliyyətləri işçilər arasında bölüşdürür və onların prosesə/avadanlıqlara sahiblənməsini təmin edir. Məsələn, mən özümə aid olan avadanlıqlara cavabdeh oluram (istehsalına, texniki xidmətinə, hətta təmizliyinə). Bu da Şərq fəlsəfəsindən qaynaqlanır; hər bir işçinin işini və avadanlığını sahiblənməsini vacib hesab edir.
Total Məhsuldar Texniki Xidmət (TMTX)-in bünövrəsini 5S metodu təşkil edir. 5S-in məqsədi yaxşı təşkil olunmuş və təmiz iş mühiti yaratmaqdır. Tək yaratmaq deyil, həm də onun davamlılığını təmin etməkdir. 5S adından məlum olduğu kimi 5 “S” hərfi ilə başlayan sözdən ibarətdir:
• Sort (Seç). İş sahəsindən lazım olmayan və istifadə edilməyən alətləri çıxar.
• Set in Order (Səliqəyə sal). Qalan əşyaları səliqəyə sal.
• Shine (Parıldat). İş yerini təmizlə və ona nəzarət et.
• Standardize (Standartlaşdır). Yuxarıdakı üç fəaliyyət üçün Standard Əməliyyat Proseduru (SƏP) hazırla.
• Sustain (Səviyyəni saxla). Əldə edilmiş nailiyyətləri qoruyub saxlamaq vacibdir. Əgər hər dəfə eyni iş zonasına 5S tətbiq edib qaydasına salmağa çalışırsınızsa deməli problem var. 5S bir dəfə təşkil edilməlidir və prosesin davamlılığı təmin edilməlidir.
5S tətbiq edilmiş sahə çox verimli olur, çünki hər avadanlığın özünün işarələnmiş yeri olur, ərazi və avadanlıqlar təmiz olur, hansısa problem baş verdikdə alətləri tapmaq asan olur. Eləcə də iş bitdikdən sonar ləvazimatlar özlərinin təyin olunmuş və işarələnmiş yerlərinə qoyulur. Və proses bu formada davam edir. Bu cür inisiativlərdə bütün kollektivin iştirakı vacibdir. Bu, bir psixologiyanın dəyişdirilməsi prosesidir və çox da asan deyil. Hər bir işçinə prosesə daxil etmək, vaxtaşırı onların fikirlərini öyrənmək vacibdir. Çünki işi görənlər operatorlar və fəhlələrdir, müdir hər dəqiqə işçilərə nəzarət edə bilməz. Bu mənada işçilər özlərinə aid olan prosesləri sahiblənməli və onun davamlı olması üçün çalışmalıdırlar. Bu, onların könlü olmazsa çətinləşir. Ona görə də Lean və xüsusilə 5S kimi inisiativlərdə onların əldə edəcəkləri faydaları da başa salmaq lazımdır. Məsələn izah etmək lazımdır ki, sən filan aləti axtarmaq üçün bütün sexi axtarırsan və vaxt itirirsən. Əgər biz 5S tətbiq edib, səliqəli iş mühiti yaratsaq sənin problemlərin azalacaq; daha rahat tapacaqsan və işi görmək üçün standard prosedurun olacaq.
Yalın istehsal tək 5S-dən ibarət deyil, bir çox fərqli, sübut olunmuş metodları var. Bunlara Kaizen (davamlı inkişaf), Value Stream Mapping (Dəyər Axınının Qrafikinin Çəkilməsi), Kanban, Visual Management (Vizual İdarəetmə), Poka Yoke kimi metodlar daxildir. Bunların hər birinin öz tətbiq sahələri var və şirkətlərə kifayət qədər xərclərə qənaət etməyə kömək edir.
Six Sigma isə beş mərhələdən ibarətdir:
1. Define – Problemi tanımla.
2. Measure – Problemin böyüklüyünü ölç.
3. Analyze – Həlli yollarını analiz et.
4. Improve – Tapdığın həllər əsasında prosesi inkişaf etdir.
5. Control – Əldə etdiyin uğurların davamlılığını təmin et.
Six Sigma sözünün özünü etimologiyası isə belədir: Normal paylanmada 6 siqma daxilində olan proseslərdə milyon məhsulda 3-4 defekt çıxa bilər. Yəni Six Sigmanın hədəfi hər bir prosesi hər milyon məhsulda maksimum 3-4 defekt çıxacaq formada dizayn etməkdir. Bunun da nəticəsi odur ki, Six Sigma tətbiq edilən sistemlər çox stabil olurlar və ölçülərdə yayılmaları az olur. Yuxarıdakı mərhələlərin hər birində statistikanın müasir yanaşmalarından istifadə edilir. Ona görə də riyaziyyat və statistika bacarıqlarının yaxşı olması mütləqdir.
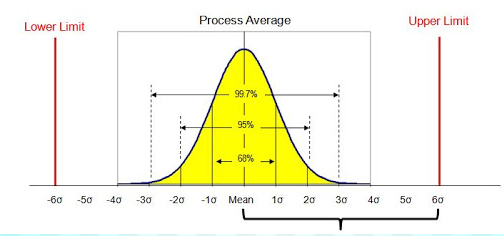
Bu yazıda Lean Six Sigma, Kütləvi İstehsaldan, onlar arasındakı fərqlərdən LSS-in metodologiyaları olan 5S və Total Məhsuldar Texniki Xidmət (TMTX)-dən danışdıq. Ümid edirik yazını oxuduqdan sonar sizdə müəyyən fikirlər formalaşdı. LSS üçün müxtəlif sertifikat proqramları var. Kurslar 4 mərhələdə aparılır: sarı kəmər, yaşıl kəmər, qara kəmər və usta qara kəmər. Bu treyninqlərə sarı kəmərdən başlayırsınız və usta qara kəmərə doğru davam edirsiniz. Adətən bu dörd kəmər fərqli modular halında olur və vəziyyətə görə bir neçə il çəkə bilər. LSS kurslarını bir çox şirkətlər təklif edirlər və hətta böyük şirkətlər özləri öz işçilərini treyninq keçərək kəmər verirlər. Qara və usta qara kəmər kifayət qədər güclü nailiyyətdir və bir çox şirkətlərin axtardıqları bacarıqlardır. Nəzərə almaq lazımdır ki, adətən təkcə sarı kəməri imtahanla keçmək olar, yaşıl kəmər və yuxarısı üçün real şirkətdə layihə keçirib həmin şirkətə müəyyən miqdarda gəlir qazandırmalısınız (və ya xərclərə qənaət etdirməlisiniz). Həmin məbləğ dəyişə bilir, məsələn mən yaşıl kəmər alarkən işlədiyim şirkətə 25 min avro qazandıran bir layihə həyata keçirmişdim.
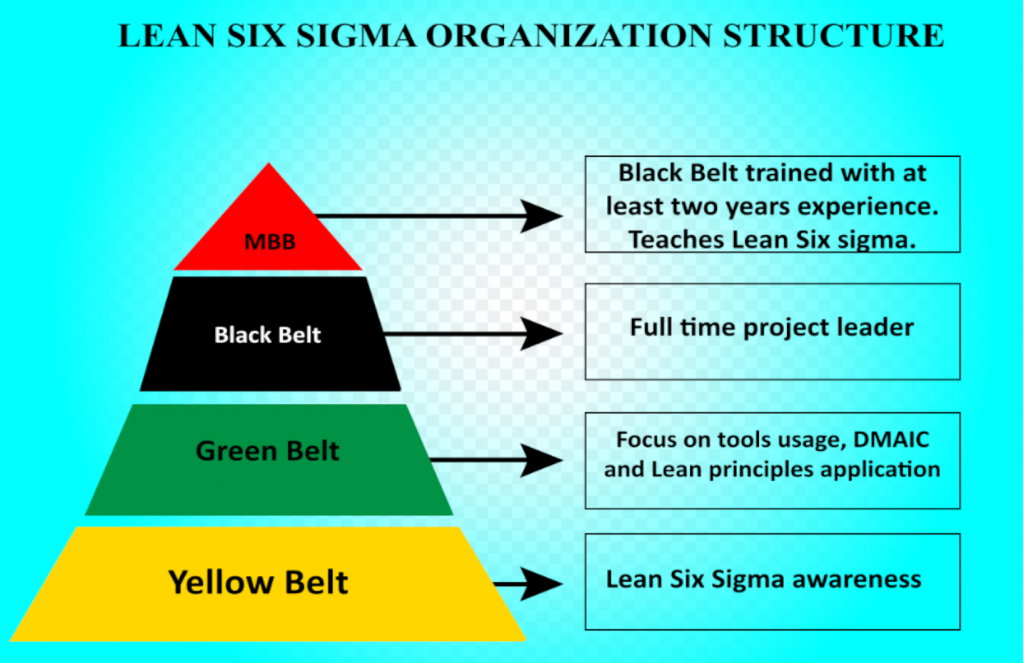
Müəllif:
Yaşar Əhmədov
HR-AZ.com portalının paylaşımlarından xəbərdar olmaq üçün rəsmi
Linkedin və
Telegram səhifələrimizi izləyə bilərsiniz.
Mənbə:
HR-AZ.com